White House "Contractor's Salvage" Revived
Architectural Elements Preserved in Private Homes on Gibson Island
Copyright © June 01, 2014 White House Historical Association. All rights reserved under international copyright conventions. No part of this article may be reproduced or utilized in any form or by any means, electronic or mechanical, including photocopying, recording, or by any information storage and retrieval system, without permission in writing from the publisher. Requests for reprint permissions should be addressed to books@whha.org
Through its long years, the White House has seen many renovations, including the most recent one that was almost total. During President Harry Truman’s renovation (1948–52), the entire interior of the White House was removed, with the exterior walls left standing. A replacement interior was fashioned entirely new. Wood removed during this renovation was generally reused or put in storage, but some of the surplus that was not reused in the renovation, or requested back by the government, found its way to several gracious homes on Gibson Island in the western Chesapeake Bay, just off the shore of Maryland.1 This is the story of these former White House architectural elements.
Much of the interior of the White House before the Truman renovation dated back to the McKim, Mead & White renovation in 1902, and some parts dated as far back as 1817–18, when the White House was rebuilt after the British infamously burned it in 1814. By Truman’s era, cuts made into load bearing beams to allow for the addition of pipes, wires, and ductwork, had compromised the structural integrity of the building. Chandeliers were swaying, floors were vibrating, and the leg of Margaret Truman’s piano actually broke through the floor.2 In addition, an inspection by the Army Corps of Engineers following the attack on Pearl Harbor in 1941 found the house to be a fire trap. The interior structure of soft brick and wood had an immense fuel accumulation in framing timbers and the dry wood lath to which the plaster walls were “locked.” President Franklin D. Roosevelt dismissed the potential solutions while he gave his attention to matters he considered more urgent.3
Convinced at last to begin a comprehensive renovation, President Truman and Congress named a special Commission on the Renovation of the Executive Mansion in June 1949. It included two senators, two representatives, and two individuals from either private life or the Executive Branch. Additional assistance came from various consulting architects and engineers. The commission was responsible for recommending the scope of the White House renovation project, choosing a general contractor, and overseeing the work to its completion. John McShain of Philadelphia was the successful bidder for general contractor, and the interior woodworking was subcontracted to Knipp & Company of Baltimore. Franklin Knipp, son of the then president of this family company, worked daily in the White House on the renovation and was soon to build a house on Gibson Island.
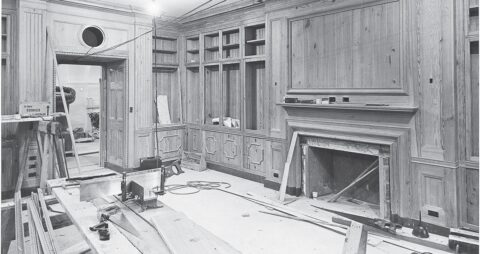
The White House Library is pictured in 1951 during the installation of the wood paneling fashioned by Knipp & Company from the old pine beams removed during the Truman renovation.
McShain’s bid was $4,880,000, and his contract to Knipp for cabinetry and millwork was $380,348.4 McShain reportedly lost twice the amount of his contract on the renovation due to a combination of factors, including escalating costs of material and labor during the Korean War and the government’s steadfast adherence to the original contract, which prevented reimbursement of extra costs even though the president and commission demanded that the work conclude with enormous speed.
McShain is sometimes referred to as “The Man Who Built Washington,” with more than one hundred important contracts including the Pentagon, the Jefferson Memorial, the Bureau of Engraving and Printing, the State Department, and the Kennedy Center for the Performing Arts.5
A Baltimore success story, John C. Knipp & Sons—as the firm was known until 1948—began as a cabinet shop in 1868. Venturing beyond its original cabinetry and carpentry focus, it expanded into the antique business, offering reproductions of historic millwork.6 Later expansions took Knipp into the marine or shipbuilding industry and high-end commercial wood interiors for buildings like the British Embassy, the National Gallery of Art, Dulles International Airport, and the United States Capitol.
The Knipp firm began working in the marine industry at the end of the Baltimore clipper ship era and continued with the new steamship era. The company focused totally on marine construction business after the outbreak of World War II, opening new woodworking shops in shipyards in New York, Savannah, New Orleans, Milwaukee, San Francisco, and Wilmington, North Carolina. Specializing in ship interiors, it won awards from the U.S. Maritime Commission and U.S. government for its wartime contributions and prodigious production. Joiner work and furniture were installed in 285 Liberty ships built at New Orleans and Savannah. Three hospital ships were completely outfitted in New York and New Jersey. Other output included 103 floating drydocks, 24 colliers, 34 AV1 vessels and 21 tankers.7 After the war, Knipp converted many passenger, merchant, and troop-carrying ships to peacetime use.
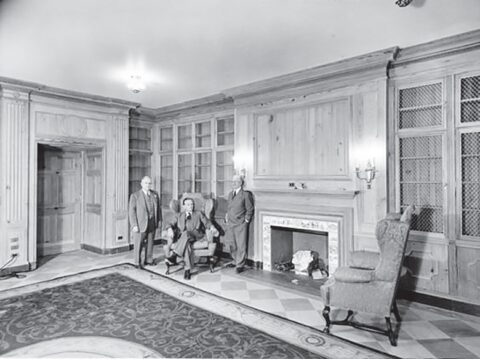
Architect Lorenzo Winslow is seated between Knipp & Company representatives Howard Knipp and B. J. Bromage in the completed room in 1952.
Because of its long history of high-end cabinetmaking, knowledge of styles and interiors, and history of providing for the needs of the White House, Knipp was a natural choice for the Truman renovation. In the late nineteenth century, the Knipp firm made a marbletopped, oak sideboard for the Family Dining Room.8 In 1909, Knipp made the furniture and cabinetry for the president’s office, including specially designed largesize chairs for President William Howard Taft.9 In 1921 the firm provided a hand-carved inaugural stand of mahogany and gilt for incoming President Warren G. Harding.10 Even the presidential yacht Williamsburg, used by Presidents Truman and Eisenhower, was outfitted by Knipp & Company. Work at the White House was welcomed by Knipp, for the marine business had slowed by the late 1940s.
As subcontractor to the original contract, Knipp & Company was very much on the scene during the dismantling of the house. It hauled away moldings, architectural elements, wood floors, and even lath under the plaster for the general contractor, who began work on December 13, 1949.
Many of the old pine beams were sawed at Knipp & Company workrooms into 4 x 4 and 6 x 4 lumber, then refashioned into unpainted paneling for four new rooms that would be rebuilt on the Ground Floor of the White House.11 Nail holes were intentionally left visible in the old wood.12 Many visitors have seen the Vermeil Room, the China Room, and the Library without realizing the origin of the wood paneling, which is painted today. A fourth paneled room by Knipp, the Map Room, is generally not on view to the public.
The oak paneling in the State Dining Room was also removed, reworked and repaired, and then reinstalled. Because diverse materials were used in the repairs, the room was painted with a pale Colonial Revival green, selected by the architect Lorenzo Winslow. The decision to paint, though in fact a practical one, broke with a fifty-year tradition of retaining the masculine-looking stained oak of Theodore Roosevelt’s day.13 The woodwork, including moldings, wainscot, hand-carvings, and trim, was fabricated for the other State Floor rooms: the East Room, the Green Room, the Blue Room, and the Red Room. The Lincoln Bedroom on the Second Floor received new millwork made by Knipp, as did many bedrooms, corridors, and sitting rooms on the Second and Third Floors.
It was President Truman’s stated intention to save “all the doors, mantels, mirrors and things of that sort so that they will go back just as they were.”14 Architect Lorenzo S. Winslow also “appreciated the old, and from the outset urged the careful conservation and reuse of paneling, window sash, molding and doors.”15 These intentions, however, were not fully realized. Some of the wood was damaged upon removal, and some was stylistically inappropriate as Winslow tried to adapt the White House interior to the time of its original architect, James Hoban. He saw to it that old materials were used when time and space allowed, in the Blue Room wainscoting for example, but in actual fact, only the State Dining Room contains much of its original wood, and that dates only to 1902. Die-pressed pine was used extensively in the renovation.16
Franklin Knipp, who became president of the firm in 1964, stressed that most of the removed millwork from the White House arrived to them unmarked, with nothing to indicate where it had come from, unless it was from a “primary” room (a State Room) or one that was to be reconstructed, such as the State Dining Room.17
Toward the end of its mandate, the Commission on the Renovation of the Executive Mansion, with the approval of President Truman, made decisions about how to dispose of materials that were removed from the White House during the renovation. Accordingly, it established the Souvenir Program.18 The commission did not want the program to be a “commercial exploitation,”19 and so it was open to all and the fees were modest. The commissioners hoped the program would be successful so, rather than mandating the reuse of as many materials as possible, they helped ensure that relics were plentiful.20
The actual distribution began in 1951 as members of the general public sent in applications of request to the Souvenir Office at Fort Myer, Virginia. The items sent out in response were raw materials such as bricks (enough to face a fireplace), nails, plaster, and small kits of wood from which gavels and canes could be fashioned. The popular program was not only self-supporting, but it made an additional $10,000 to aid the renovation. The American people delighted in owning bits and pieces of their national symbol, the White House, and were willing to pay anywhere from 25 cents to $5.00 for the privilege.21
White House moldings that were not reused in the White House reconstruction but left stored with the Knipp firm were originally intended by the firm to be returned to the White House, until at last Major General Glen E. Edgerton, the government’s representative on the work, ordered Knipp to stop bringing back the old wood.22 At that point the wood became “contractor’s salvage,” owned by the contractor. General Edgerton was cleaning house. After the White House was fully rebuilt, disposing of excess material not used in the Souvenir Program and considered trash was a challenge. This material—wood, bricks, metal parts, and plastic—ended up in diverse places such as the woodwork shop in the Lorton, Virginia, facility of the District of Columbia Department of Corrections. The most by far was at Fort Myer, Virginia, which was used as landfill.23 The wood that remained in the Knipp & Company’s Baltimore warehouse, the only scrap that was now preserved, was stored until the company closed its doors in the late 1990s. The government had never approached Knipp about the scrap, but out of a feeling of obligation for the historic material, Franklin Knipp offered to return what remained of the surplus to the White House himself. A later generation was more interested.
In 1988 National Park Service architectural conservators scientifically analyzed some of the wood returned by Knipp. Blue Room window and door trim seem to be from both 1817–18 and later dates, judging from the paint layers.24 In 2000, surviving East Room shutters were dated to 1817–18, while a wood panel from a dado or wainscot was likely from 1902.25
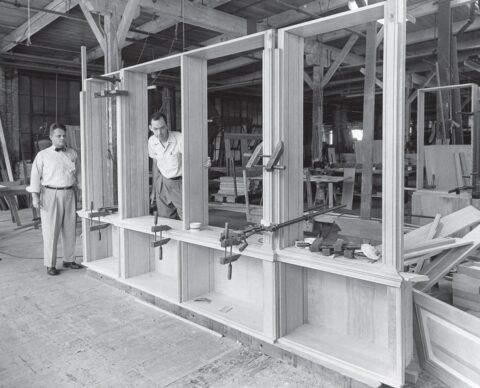
Charles Knipp, a brother in the Knipp family business, and George Kessler pose with bookcases under construction in the Knipp facility in 1951. The bookcases would be installed in the Second Floor corridor in the White House.
The transfer of the surplus back to the White House—a donation from Knipp—took place in 1996. In the meantime, Knipp had used some of the “contractor salvage” wood in his own home on Gibson Island and offered small quantities to friends there as well. It is difficult to trace the precise origin of the Gibson Island wood elements, but old White House interior photographs show moldings, rosettes, and shutters that look very similar or identical to what is in the Gibson Island homes. Moreover, some of the Gibson Island homes have small metal plaques stating where the wood may have been located in the White House. These plaques may not be reliable, however, and, given the passage of time, it is nearly impossible to be precise regarding the origin of the elements. It does seem that most of the wood elements date to 1902, and some are as early as 1817–18.
Franklin and Eleanor Knipp built their house on Gibson Island around 1958. In 1985, before they sold their house to Leonard and Eileen Mitchard, they were able to use some of the leftover White House wood in a remodeling project.26 Although Franklin was a skilled carpenter with a woodworking shop in the basement of his Gibson Island home, he probably did not fashion all of the woodwork himself.27
A white-painted bifold door in the front hall of the house is made from interior shutters possibly taken from the Second Floor of the White House. That the shutters are mahogany is consistent with the fact that mahogany was used in the 1817–18 rebuilding of the White House.28 Old White House photographs do show similar interior shutters.
Crown moldings, window valances, and a fireplace mantel constructed from the reclaimed lengths of wood are in the living room of the Knipp house. The crown moldings have dental trim, which could possibly have come from the East Room. The window valances were supposedly taken from the Family Dining Room on the State Floor of the White House, according to Knipp’s plaque:
"Window valances in the Living Room at Gibson Island were made from the chair rail from the Family Dining Room of the White House in 1952. (originally fabricated about 1850)"
It has not been possible to verify the chair rail in old White House photographs. The Knipp dining room contains wainscot that is also identified:
"Pine wainscoating [sic] installed in the White House about 1850, removed from the White House during the 1952 renovation, and refurbished and installed in Gibson Island house about 1985."
The date 1850 on Knipp’s plaques seems unwarranted as the wood was likely installed in 1902 or possibly in 1817–18.29 A 1947 photograph of the White House family quarters shows wainscot in the same style. The Knipps no longer live on Gibson Island but do retain a few souvenirs of White House wood, including a gavel and a small pine box with a fitted tray. Several of their friends who were renovating their homes on Gibson Island received, as gifts, lengths of White House molding to use in their remodeling. Typically, these were made into fireplace mantels. The Harrison and Barbara Stone house mantel is identified with a plaque provided by Franklin Knipp:
"Molding from the Green Room White House 1951, Donated by H. Franklin Knipp Jr 1981."
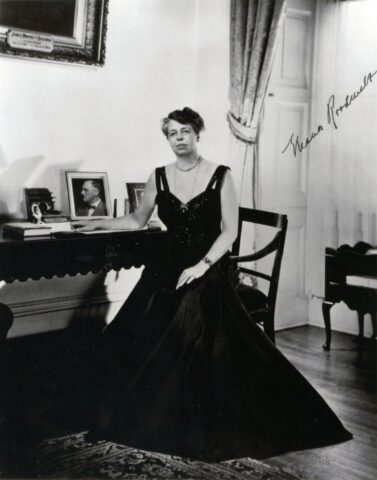
A photograph of Eleanor Roosevelt in the Second Floor Monroe Room, now known as the Treaty Room, reveals shutters similar to those used in the Knipp house as bifold doors and believed to date from the reconstruction of the White House, 1815–17
Library of CongressThe Claude and Marian Bureau house has a fireplace mantel made of White House molding, although it is not identified with a plaque. Mrs. Bureau remembered that it was fashioned about 1990, one of the last mantels from White House molding to be installed. It is quite similar in form or profile to the Stones’ mantel. Sally and Richard Henderson also used White House moldings offered to them by their friend Franklin Knipp for a 1983 remodeling project in their Gibson Island home, one of the three oldest on the Island. They used it to fashion a mantel over a wood-burning stove. Another molding was used in a fireplace mantel by Brian and Beverly Rogers when they built a new house on the island in the 1990s. Rogers remembers that Franklin Knipp “came over one afternoon with a board that still had nails hanging out of it. It was a nasty board—if you saw it on the beach you wouldn’t have picked it up. I thought, ‘I am going to put this old board in my new house?’ Most of the paint was stripped but it had a little light red around it.”30
Henry and Nancy Hopkins have molding that was used to make a door surround in their front hall. Franklin Knipp told Hopkins that the wood came from the Red Room, and indeed the wood had a small section of red fabric attached to the back. The White House wood includes both vertical pieces and the lower part of the horizontal overdoor piece, but the crown part of the molding is not White House wood. Another small run of wood, about 3 feet long, was incorporated into the molding surrounding the Hopkins’ front door. It was not unusual for the White House moldings to be incorporated with other wood trim when owners fashioned exactly what they wanted or needed to add parts for completion. Hopkins explained:
"Franklin came over to our house on Skywater and brought with him a piece of molding and the book on the White House rebuild. He told me the story about how his first job at Knipp and Company had been the White House renovation. He told me he had stored some of the molding in the basement of their house. He told me the piece came from the White House’s Red Room and noted the piece of red cloth still attached to the molding as a piece of the cloth wall covering. He then went on to explain how Knipp and Company had stored all the old molding all these years. . . . The 3 foot piece of molding was [used] as the molding in the formal part of our house and is part on the lintel over the front door. . . . As to why Franklin gave us the molding, he knew we were building our new house and thought we might like to have a piece of the White House molding to use as model for the molding we might choose. And that is exactly what we did. The idea was entirely his."31
Helen and Bill Passano are Gibson Island residents with another home in Baltimore, which has a fireplace mantel made with trim given to them by Franklin Knipp. The plaque affixed to their mantel reads:
"Mantel Made from Original Door Trim Removed from the White House in 1950."
Franklin Knipp also made bookends from rosettes that were originally part of White House door trim and gave them to the Passanos’ then son-in-law, Thomas Ford. Similar rosettes can be seen in standard door and window frames in many old photographs of the White House, including photographs of the Yellow Oval Room on the Second Floor and the Blue Room on the State Floor. The bookends have paper Knipp & Company labels. Ford also has panels of unpainted wood that were hand-hewn for making wainscot, very similar to the wainscot in the Knipp house. Ford has fashioned more White House molding into a support for an antique clock and an unpainted cornice over a window.32
The White family received wood in 1973 from Knipp, which Harold White helped make into a mantel when he and Harriet bought their house on Gibson Island. The Whites’ fireplace surround was fashioned from panels with raised sections that were likely interior shutters at the White House at one time. Their son John White grew up on Gibson Island, explaining that “my Dad ran the boat yard from 1967 to 1985 . . . there were a lot of wood boats and therefore carpenters.” In addition to the mantel, Harold White fashioned White House woodwork into little boxes and small woodworking projects.33
Sixty years after the Truman renovation of the White House, very few people are left who remember and were involved in the distribution of unwanted surplus materials from the president’s house. However, wood salvaged from the renovation still lives on in new surroundings.